Molder Enterprise – Making Molds for Manufacturing
Molder Enterprise is a mold-maker in Thailand for commercial manufacturing processes. The process of mold-making is an ancient craft, handed down over the generations.
As technology has improved the manufacturing process, the mold-makers skills have had to keep improving as well. Molder Enterprise has kept pace with this increasing technology and embraced the latest in mold manufacturing processes to significantly reduce the waste generated in die-casting, injection molding, double injection molding and rubber compression molding.
We are a Thai mold maker that has been in business since 1996. Our molds are widely used in aluminium/zinc die-casting factories, rubber parts manufacturing, and the Thailand plastic injection molding industry for all types of manufacturers.
Before a simple or complicated part can be created in a production line, a perfect mold has to be made to produce the part.
Each mold can be thought of as a ‘reverse image’ of the part for which the mold is intended. It has to simulate the part exactly down to the smallest detail. Because the mold is used repeatedly to mass-produce parts, the slightest error in it can cost the manufacturer dearly if it contains any flaws or errors.
Products
Creativity, Experience and Engineering Ability
The creation of a mold for mass-production is a complicated process which takes a combination of creativity, experience and engineering ability.
The manufacturer generally delivers a prototype of the part desired to the mold maker in Thailand, along with CAD drawings of the part. It is then our responsibility to create a mold that can be used over and over to quickly and precisely replicate the part, saving the manufacturer the time and expense of creating each part by hand.
Plastic Thailand injection molding, blow molding, rubber compression, rubber injection, and Aluminium/Zinc die-cast molding are the techniques used to create exact replicas of the desired part or finished product. We can provide the molds themselves or we can supply the entire plastic injection molding process as well.
We service all of our customers of various different manufacturing industries with the same level of dedication, experience and attention to detail.
A Trusted Mold Maker in Thailand
Our technicians and engineers have more than 20 years of experience making custom molds for the automotive, rubber, plastics and metal manufacturing industries. Our customers rely on our experience, skills and dedication to create every mold correctly down to the finest detail and to meet every tolerance down to the millimetre. We are one of the premier Thailand plastic injection molding companies.
Plastic Injection molding is a manufacturing process designed to produce large volumes of parts with little to no material waste. It is superior to the CNC machining process that carves away significant portions of a block of material, creating significant amounts of wasted material.
We use only the latest software and advanced machinery to create our molds. Our products have been certified as ISO 9001:2015 compliant. We work with customers all over Thailand, providing them with expert molds and molding processes.
Simplify Your Manufacturing Process
There is a difference between designing a product and designing a product that can be relatively simple to manufacture. The small details in the product can determine the manufacturing process and the structure of the mold, thus affect the tooling cost.
We can guide you through the process of mold making and casting to provide you with an alternative and simpler method to consider in your manufacturing process. Contact us today to learn how much easier and cost effective the mold making and casting process can be for your production line.
A Quality Product
Moreover, Plastic injection molding in Thailand is a manufacturing process which produces molds via liquid injection. It is most commonly performed with thermoplastic polymers (i.e., Polypropylene, ABS, Polyethylene, Polystyrene). Plastic injection moulding creates a high volume of consistent, high-quality units. When manufactured in large volume, injection molding has an extremely low cost per unit
However, keep in mind that up-front costs for injection molding in Thailand tend to be high because of costs associated with design, testing, and tooling requirements (i.e., complexity, materials, accuracy, etc.); therefore it’s essential the design is right the first time.
You can save the costs by combining different materials into the same part for greater utility with fewer assembly processes. With 2 shot injection molding, you can use a hard and a soft plastic to create a sealing edge and/or use two different colors. Similarly, insert molding allows a non-plastic component, such as a metal screw, to be incorporated into the design.
We are trusted for over 25 years, building trustful and
long lasting relationship with our customers.
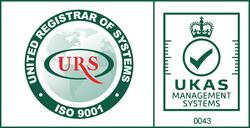
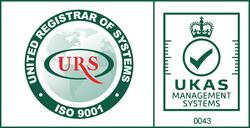
Looking for mold manufacturing, mold making, and plastic injection molding services in Thailand? For more information about our services in Thailand, please contact Molder Enterprise.
Tel: 034-476-173, 034-476-174, 09-827-039-09 and 063-198-0988
Email: molder113_3@hotmail.com